KRR045DLS1820NNK3C2NRA6NAAANNNNNN sauer danfoss pump
KRR045DLS1820NNK3C2NRA6NAAANNNNNN sauer danfoss pump
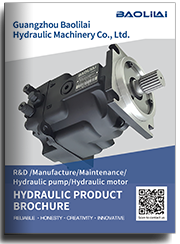
- Product Details
- Applicable Scene
In the realm of CNC (Computer Numerical Control) and precision manufacturing, hydraulic oil pumps play a pivotal role in ensuring efficiency, accuracy, and reliability. These pumps are fundamental components that facilitate the movement and operation of various machinery used in manufacturing processes. This article delves into the design considerations and innovations in hydraulic oil pumps that are tailored specifically for CNC and precision manufacturing tools.
KR-R-045D-LS-18-20-NN-K-3-C2NR-A6N-AAA-NNN-NNN
KRR045DLS1820NNK3C2NRA6NAAANNNNNN
One of the primary functions of hydraulic oil pumps is to convert mechanical energy into hydraulic energy, which is then used to perform work in machinery. The design of these pumps needs to cater to several critical factors, including flow rate, pressure requirements, heat dissipation, and the specific operational needs of the CNC machines they serve.
83048070
Firstly, the flow rate is a crucial factor in pump design. Different CNC machines have distinct hydraulic flow requirements based on their size and the complexity of the operations they perform. For example, milling machines may require a high flow rate for efficient chip removal and tool cooling, whereas lathes may need a more moderate flow rate for precision tasks. Therefore, pump designers must conduct thorough analysis and calculations to ensure that the pump can consistently deliver the required flow under varying operational conditions.
Another essential consideration is the pressure requirements of the hydraulic system. CNC machines often operate under high pressure to achieve precise movements and maintain tool stability. The hydraulic pump design must accommodate these high-pressure demands while ensuring operational safety. This necessitates the use of high-quality materials and robust construction techniques to withstand the stress and prevent leaks or failures.
Heat management is also a critical aspect of pump design. During operation, hydraulic oil can generate a significant amount of heat, which can adversely affect the performance of both the pump and the CNC machinery. Efficient heat exchange systems, such as cooling jackets or external heat exchangers, can be integrated into the pump design to maintain optimal operating temperatures. Additionally, selecting the right hydraulic fluid with appropriate viscosity can aid in reducing heat generation and improving overall efficiency.
Moreover, advancements in technology have paved the way for integrating smart features into hydraulic pump design. The incorporation of IoT (Internet of Things) sensors can provide real-time monitoring of pump performance, allowing for predictive maintenance and ensuring optimal operation. These sensors can track parameters such as temperature, pressure, and flow rate, providing manufacturers with vital data to optimize their CNC operations and minimize downtime.
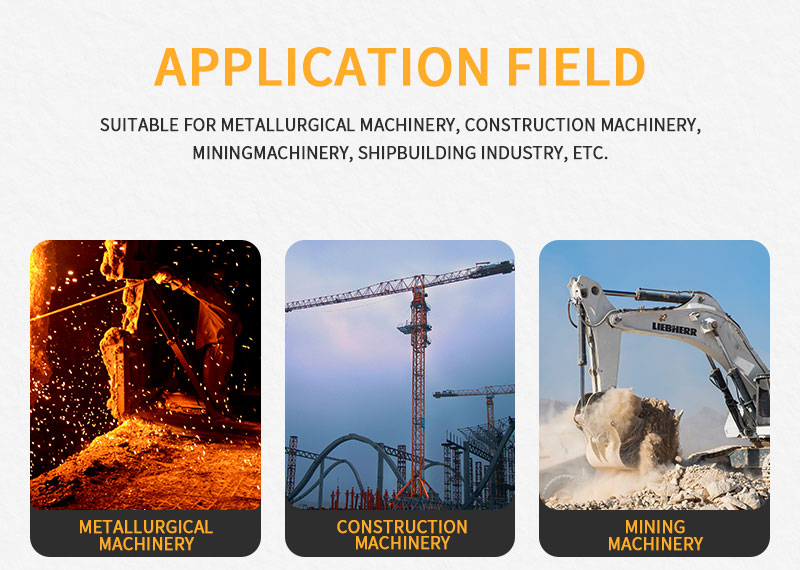
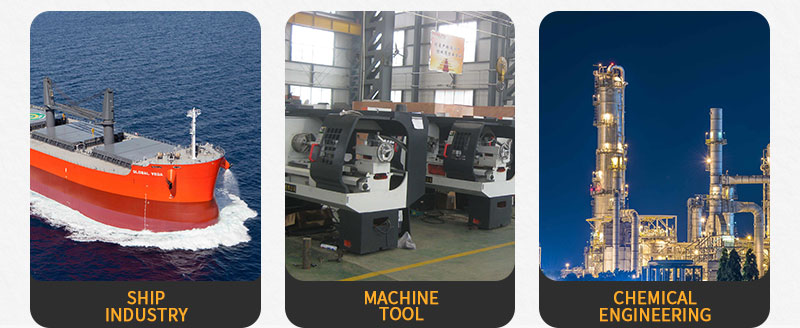