KRR045DLS2125NNN3C2NFA6NPLBNNNNNN danfoss pump
KRR045DLS2125NNN3C2NFA6NPLBNNNNNN danfoss pump
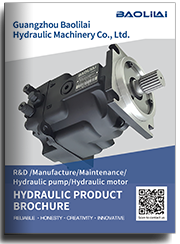
- Product Details
- Applicable Scene
The integration of hydraulic systems in wind power technology is increasingly gaining attention due to their efficiency and reliability. Among these systems, hydraulic accumulators play a critical role in energy storage and management, ensuring that wind turbines can operate smoothly even in variable wind conditions. This article explores the design considerations and technical specifications for hydraulic oil pumps that serve hydraulic accumulators in wind power systems.
KR-R-045D-LS-21-25-NN-N-3-C2NF-A6N-PLB-NNN-NNN
KRR045DLS2125NNN3C2NFA6NPLBNNNNNN
Hydraulic accumulators function as energy storage devices that can absorb and release energy as needed, providing a buffer for fluctuating energy inputs and demands. These accumulators typically use hydraulic fluid to store energy under pressure. The role of hydraulic oil pumps in this system is to move the hydraulic fluid into and out of the accumulators as required, thus maintaining optimal pressure levels and system efficiency.
7004208
One of the first considerations in designing hydraulic oil pumps for this application is the selection of the pump type. Common choices include gear pumps, vane pumps, and piston pumps. Each type has its benefits; however, for wind power systems that may require high efficiency and the ability to handle varying flow rates, gear pumps are often favored due to their compact size and reliability.
Another key design factor is the pump’s capacity and pressure ratings. Wind power systems can operate under a wide range of pressure conditions, depending on the specific design of the turbine and the hydraulic accumulator. It is essential to ensure that the pump can achieve the required pressure ratings while maintaining a high flow rate. As hydraulic systems can generate significant heat, incorporating efficient cooling mechanisms into the pump design is also vital to prevent overheating and maintain optimal performance.
Material selection is equally critical in the design of hydraulic oil pumps. Given that wind power systems are often exposed to harsh environmental conditions, materials must be chosen for their durability and resistance to corrosion. Common materials include high-strength steel and certain composites that can withstand fluctuating temperatures and moisture.
Moreover, the design of hydraulic oil pumps must take into account maintenance considerations. Pumps that are easy to service can help minimize downtime and reduce operational costs. This involves incorporating features such as easy access to critical components and the use of standard parts that facilitate repairs and replacements.
Integration with control systems is another crucial aspect of pump design. Modern wind power systems utilize sophisticated control technologies to optimize performance. The hydraulic oil pumps should be designed to interface seamlessly with these control systems, allowing for precise regulation of fluid flow and pressure in response to changing operational demands.
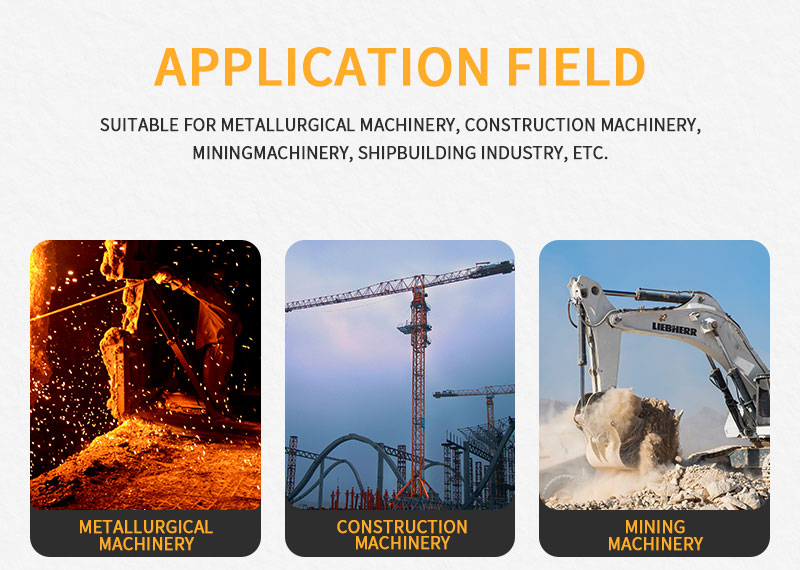
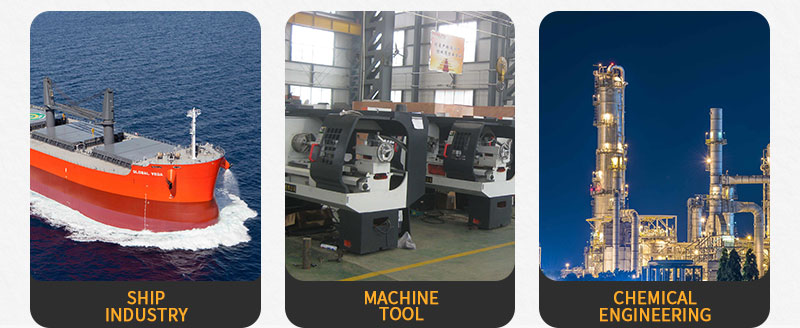