KRR045DLB2114NNN3C2NFA6NPLBNNNNNN hydraulic pump
KRR045DLB2114NNN3C2NFA6NPLBNNNNNN hydraulic pump
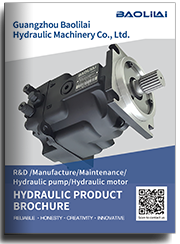
- Product Details
- Applicable Scene
Hydraulic systems play a crucial role in various industries, serving as the backbone for machinery and equipment operations. Within these systems, the hydraulic fluid is vital for transferring power and ensuring efficient performance. For those using Sauer Danfoss pumps, maintaining hydraulic fluid quality is essential for maximizing performance and longevity. Here are some best practices for hydraulic fluid maintenance in Sauer Danfoss pumps.
KR-R-045D-LB-21-14-NN-N-3-C2NF-A6N-PLB-NNN-NNN
KRR045DLB2114NNN3C2NFA6NPLBNNNNNN
Proper Fluid Selection
7004268S
Choosing the right hydraulic fluid is the first step toward effective maintenance. Sauer Danfoss pumps are designed to work optimally with specific types of hydraulic fluids. Always refer to the manufacturer’s guidelines to select fluid that meets the required viscosity, temperature range, and chemical compatibility. Using the wrong fluid can lead to reduced performance and increased wear of pump components.
Regular Fluid Sampling and Analysis
Routine sampling and analysis of hydraulic fluid can help identify potential issues before they lead to significant problems. Periodic testing measures factors such as viscosity, contamination levels, acidity, and the presence of wear particles. A detailed analysis will provide insights into fluid health and enable operators to make informed decisions about fluid replacement or treatment.
Contamination Control
Contamination is one of the leading causes of hydraulic system failure. Dust, dirt, water, and metallic particles can degrade fluid quality and lead to pump damage. To minimize contamination, implement a strict cleanliness protocol during fluid changes, including using clean tools and containers. Storing hydraulic fluids in sealed and dust-free environments can also help maintain fluid integrity.
Monitoring Temperature and Pressure
Regularly monitoring the temperature and pressure within the hydraulic system is vital for ensuring optimal performance. Elevated temperatures can lead to reduced fluid viscosity and increased wear, while pressure anomalies can indicate impending faults. Installing temperature and pressure gauges provides valuable data that ensures operators can take swift action if readings deviate from normal ranges.
Routine Maintenance and Changes
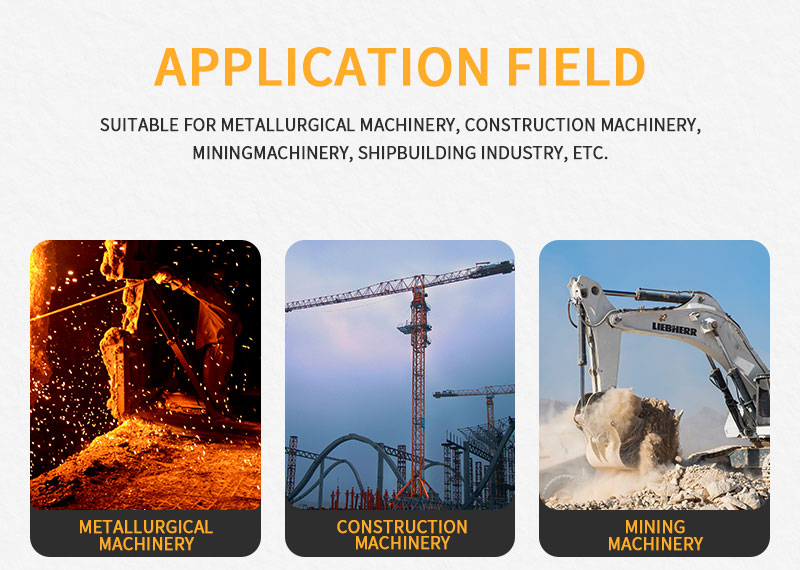
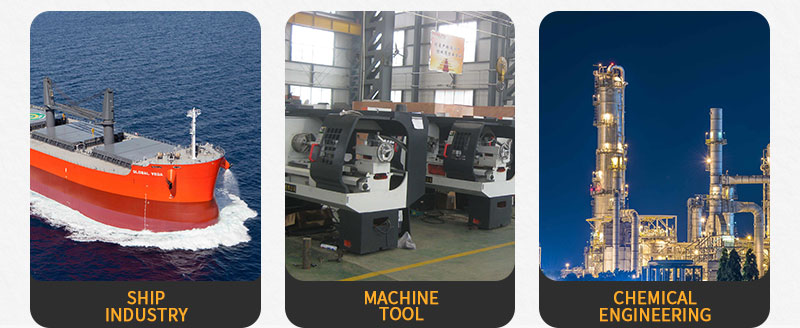