KRR045DLS2120NNN3K2BGA6NAAANNNNNN high pressure pump
KRR045DLS2120NNN3K2BGA6NAAANNNNNN high pressure pump
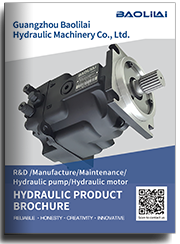
- Product Details
- Applicable Scene
In the realm of maritime safety, firefighting systems aboard ships hold a critical role in protecting lives and property. One of the pivotal components of these systems is the hydraulic oil pump, which facilitates the transfer and pressurization of water necessary to combat onboard fires effectively. This article explores the design considerations and challenges associated with hydraulic oil pumps in high-pressure water systems specifically tailored for maritime firefighting.
KR-R-045D-LS-21-20-NN-N-3-K2BG-A6N-AAA-NNN-NNN
KRR045DLS2120NNN3K2BGA6NAAANNNNNN
The primary function of hydraulic oil pumps in firefighting systems is to deliver a reliable and efficient flow of water at high pressures. This necessitates a robust and well-engineered design capable of withstanding the harsh marine environment while meeting the stringent demands of firefighting operations. Several factors must be taken into account when designing these pumps.
83010829
Firstly, the operating pressure is a critical consideration. Firefighting systems typically require high-pressure outputs, often exceeding 8 to 10 bar (approximately 116 to 145 psi) to ensure effective water jet delivery. The pump must be designed to handle these pressure levels continuously, which necessitates the use of high-strength materials for the pump casing and internal components.
Moreover, corrosion resistance is vital given the marine environment. The materials selected for pump construction must be resistant to seawater, humidity, and other potential corrosive elements. Stainless steel and specialized coatings are often employed to enhance durability and extend the life of the pump.
Another important aspect of pump design is efficiency. The hydraulic oil pump should operate efficiently to minimize energy consumption while maximizing the output flow rate. This requires precise engineering of the pump’s internal geometries, including the impeller or rotor design, to reduce hydraulic losses and improve performance.
Additionally, the pump should feature a reliable sealing system to prevent leaks, which could not only reduce efficiency but also pose environmental risks. The choice of seals must consider the operating pressure and temperature ranges, as well as compatibility with hydraulic fluids used in maritime applications.
User-friendliness is also a paramount consideration. Maintenance accessibility plays a significant role in the design process, as onboard maintenance conditions can be challenging. The pump should be designed for easy disassembly and reassembly, allowing crew members to conduct routine maintenance checks and necessary repairs without extensive downtime.
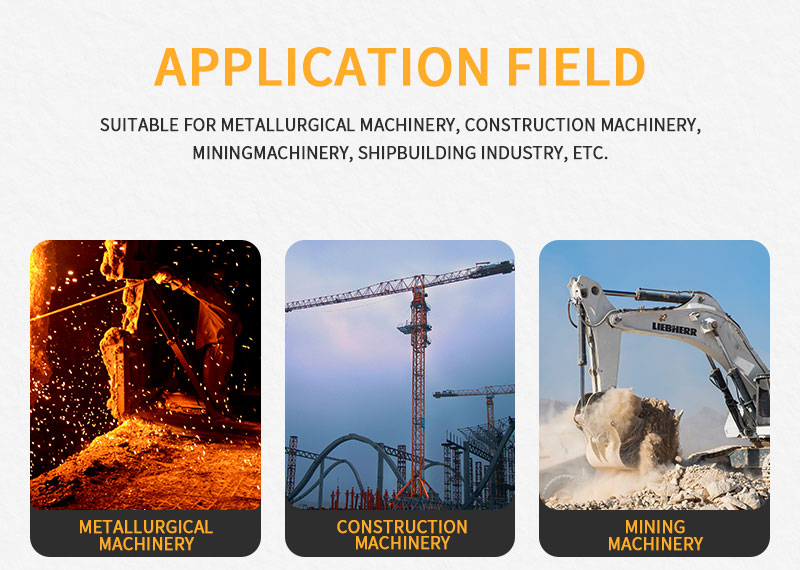
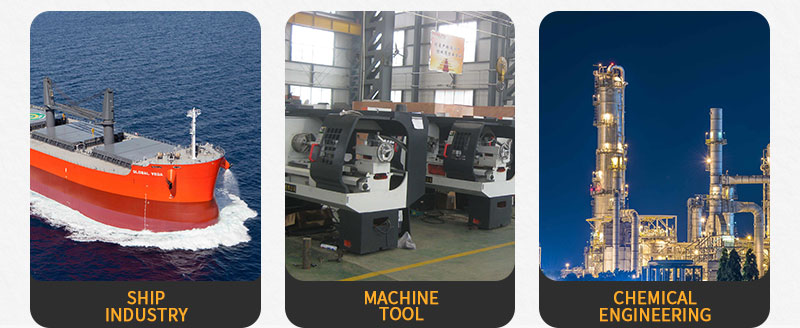