90L100DD5BC80S4S1FG1GBA424220 hydraulic pump
90L100DD5BC80S4S1FG1GBA424220 hydraulic pump
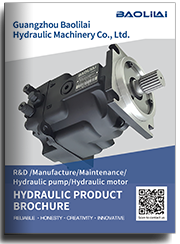
- Product Details
- Applicable Scene
In modern power plants, control systems play a crucial role in managing operations efficiently and safely. One of the vital components of these control systems is the hydraulic actuation mechanism, which relies heavily on hydraulic oil pumps. Understanding the relationship between hydraulic oil pumps and hydraulic actuators is essential for optimizing functionality and reliability in power plant operations.
90L100-DD-5-BC-80-S-4-S1-F-G1-GBA-42-42-20
90L100DD5BC80S4S1FG1GBA424220
Hydraulic systems utilize incompressible fluids, typically hydraulic oil, to transmit power from one location to another. The hydraulic oil pump serves as the heart of this system, pressurizing the oil and supplying it to the hydraulic actuators. These actuators convert the hydraulic energy into mechanical work, enabling them to perform tasks such as opening and closing valves, adjusting turbine blades, or raising and lowering equipment.
701527
The process begins when the hydraulic oil pump generates pressure by drawing oil from a reservoir and forcing it through a series of valves and hoses into the hydraulic actuators. The design of the pump—whether gear, vane, or piston—determines the flow rate and pressure generated, which directly influences the performance of the actuators. For instance, a gear pump may provide a steady flow for applications requiring consistent motion, while a piston pump can deliver higher pressures for heavy-duty tasks.
Once the hydraulic oil reaches the actuator, it enters a cylinder where mechanical movement occurs. The oil’s pressure forces a piston within the cylinder to move, thereby creating linear motion. This movement can be harnessed to perform a variety of actions in the power plant. For instance, actuators can be connected to valves in cooling systems, regulating water flow and temperature, or to automated systems managing coal feed or turbine control.
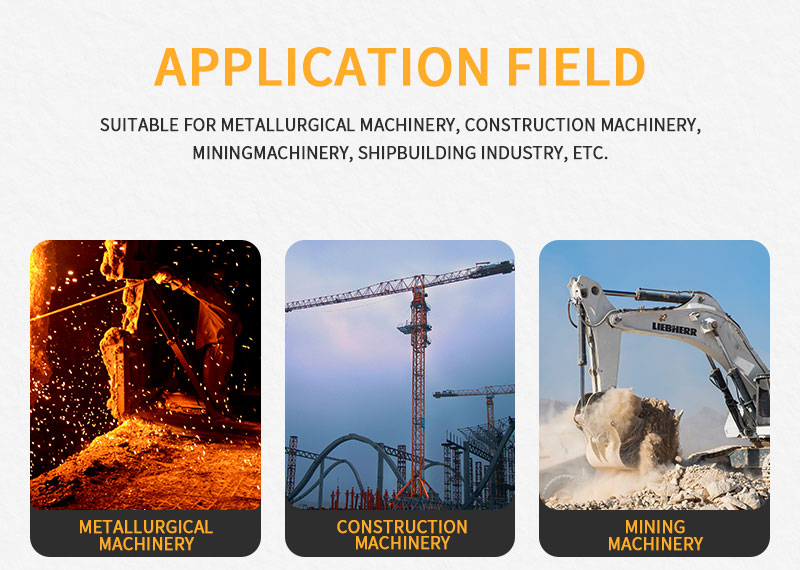
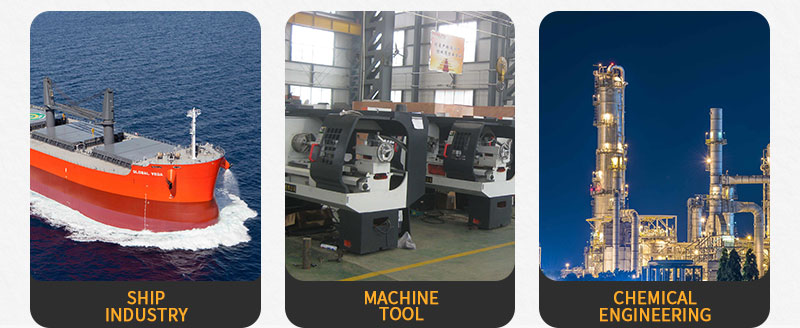