90L130MA1DE80P3F1F09GBA454520 sauer danfoss pump
90L130MA1DE80P3F1F09GBA454520 sauer danfoss pump
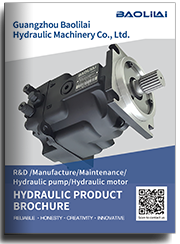
- Product Details
- Applicable Scene
Hydraulic systems are essential in many industrial applications, providing the power necessary for a wide range of operations. However, one of the significant challenges faced by these systems, especially in high-temperature environments, is the risk of hydraulic pump failures. Such failures can lead to costly downtime, decreased productivity, and safety hazards. This article offers strategies to prevent hydraulic pump failures in high-temperature hydraulic systems.
90-L-130-MA-1-DE-80-P-3-F1-F-09-GBA-45-45-20
90L130MA1DE80P3F1F09GBA454520
Understanding the causes of hydraulic pump failures is the first step in prevention. High temperatures can drastically affect hydraulic fluids, leading to degradation and reduced lubrication properties. This degradation can create varnish buildup and cause pump components to wear prematurely. Therefore, selecting the right hydraulic fluid is essential. Fluids with higher thermal stability and a broader operating temperature range can withstand the heat and maintain their properties under stress. Synthetic hydraulic fluids, for instance, offer better resistance to degradation compared to traditional mineral oils.
513851
Maintaining optimal operating conditions is also crucial. Regularly monitoring the temperature of the hydraulic fluid is essential for identifying potential issues before they lead to pump failure. Implementing temperature sensors and alarms can help keep the system within safe operating limits. Additionally, proper ventilation and cooling systems can help dissipate excess heat. Using heat exchangers to maintain a more stable temperature can be effective in high-demand applications.
Another important aspect is regular maintenance. Establishing a routine maintenance schedule that includes checking fluid levels, filters, and overall system performance can help identify problems early. Changing the hydraulic fluid regularly, according to the fluid manufacturer’s recommendations, can prevent the buildup of contaminants and degradation products. Moreover, ensuring that all components, including seals and fittings, are in good condition will minimize leaks and pressure losses.
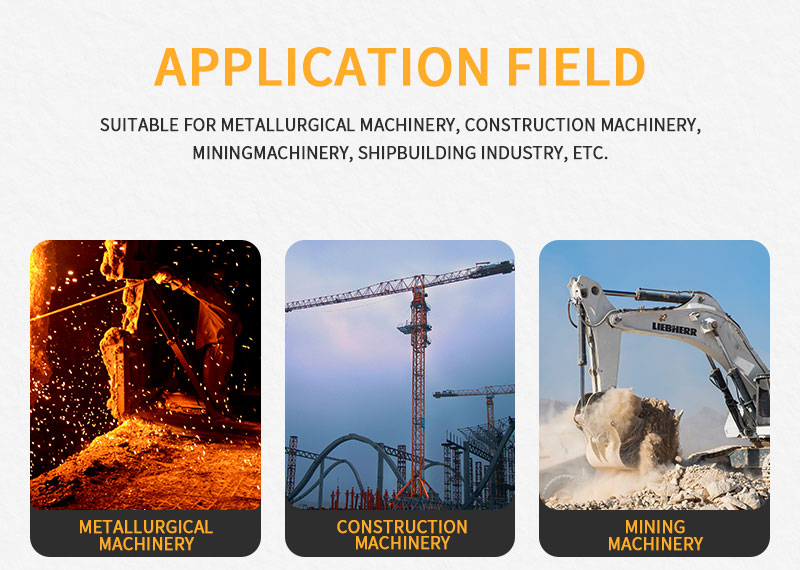
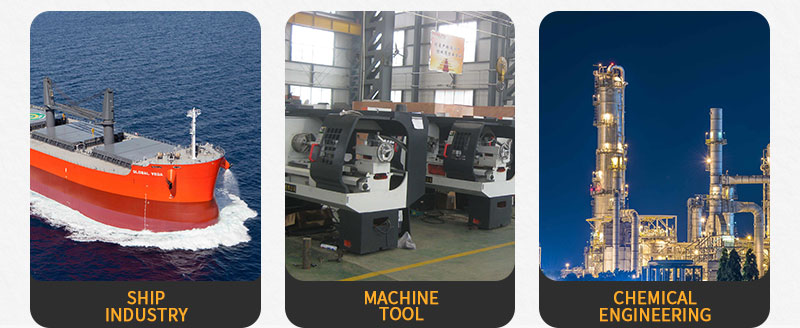