90R075KA5NN80P3C7D03GBA232324 high pressure pump
90R075KA5NN80P3C7D03GBA232324 high pressure pump
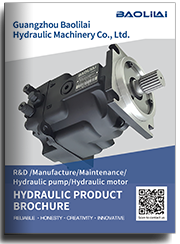
- Product Details
- Applicable Scene
High-pressure chemical synthesis is a critical process in various industries, including pharmaceuticals, petrochemicals, and materials science. The efficiency and reliability of this process depend significantly on the equipment used, particularly the pumps that deliver the reactants under high pressure. Among the various types of pumps available, plunger pumps stand out for their ability to handle the demanding requirements of high-pressure applications.
90-R-075-KA-5-NN-80-P-3-C7-D-03-GBA-23-23-24
90R075KA5NN80P3C7D03GBA232324
Plunger pumps, also known as positive displacement pumps, operate by utilizing a piston (plunger) that moves back and forth within a cylinder. This movement creates a vacuum that draws in fluid from the inlet, which is then expelled through the outlet under high pressure. Their design allows for precise control over flow rates, making them suitable for applications where accurate dosing of chemicals is essential.
83029782
One of the primary advantages of plunger pumps in high-pressure chemical synthesis is their ability to generate and maintain high pressures. These pumps can reach pressures well above 30,000 psi, making them ideal for processes that require extreme conditions. The robust design of plunger pumps minimizes the risk of leaks and ensures the integrity of the chemical synthesis process, which is crucial when dealing with hazardous materials.
In addition to their high-pressure capabilities, plunger pumps are noted for their versatility. They can handle a wide range of fluids, including corrosive chemicals and slurries, thanks to the selection of materials and seals available. This adaptability is particularly important in chemical synthesis, where the properties of reactants can vary dramatically.
Maintenance and reliability are also key considerations in high-pressure chemical systems. Plunger pumps typically have fewer moving parts than other pump types, which translates to reduced wear and tear and lower maintenance requirements. Regular maintenance and monitoring can further enhance their longevity and operational efficiency, minimizing downtime in critical processes.
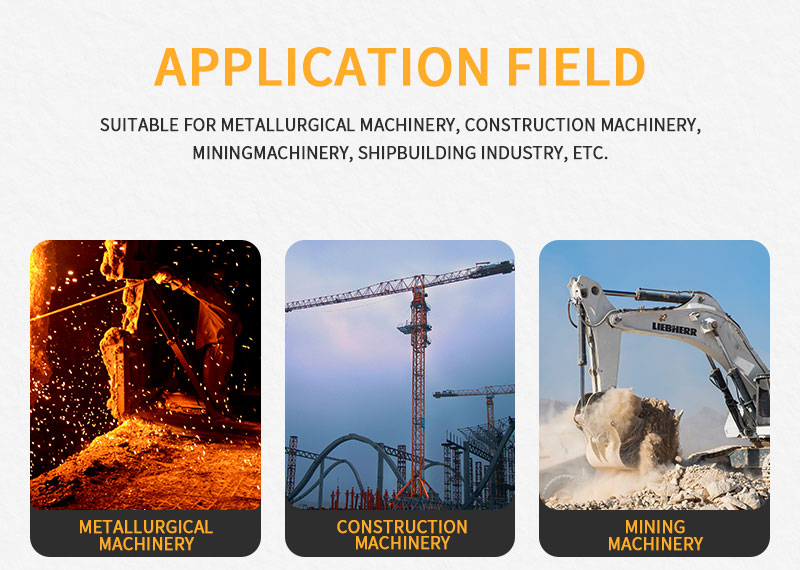
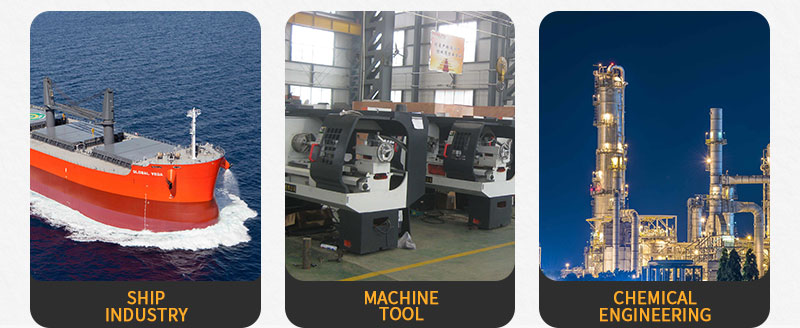