LRR030DPC19NNNNN3C2NGA6NKNBNNNNNN piston pump
LRR030DPC19NNNNN3C2NGA6NKNBNNNNNN piston pump
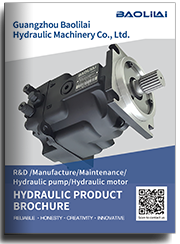
- Product Details
- Applicable Scene
In the highly competitive field of hydraulic pump manufacturing, organizations like Danfoss need to implement effective Key Performance Indicators (KPIs) to measure and enhance their operational efficiency, product quality, and customer satisfaction. KPIs are crucial metrics that help track progress towards business objectives and drive continuous improvement. Below are some critical KPIs relevant to Danfoss hydraulic pumps.
LR-R-030D-PC-19-NN-NN-N-3-C2NG-A6N-KNB-NNN-NNN
LRR030DPC19NNNNN3C2NGA6NKNBNNNNNN
One of the most essential KPIs for Danfoss hydraulic pumps is the Product Reliability Rate. This metric evaluates the performance and reliability of hydraulic pumps in real-world applications. A higher reliability rate indicates that the pumps meet customer expectations and function as intended without frequent malfunctions. Monitoring this KPI helps Danfoss identify areas for product improvements and enhances its reputation in the marketplace.
83045731
Another vital KPI is the Mean Time Between Failures (MTBF). This indicator measures the average time elapsed between pump failures during operation. A longer MTBF suggests a more reliable product and reflects the effectiveness of production and quality control processes. By tracking MTBF, Danfoss can refine their manufacturing practices and invest in better-quality materials, ultimately leading to fewer failures and increased customer satisfaction.
The Customer Satisfaction Index is also a cornerstone KPI for Danfoss. Gathering feedback through surveys and customer reviews allows the company to measure how well its hydraulic pumps meet user expectations. A high customer satisfaction score not only indicates product performance but also highlights the effectiveness of after-sales support and customer service. Addressing areas of concern can lead to improved customer loyalty and increased repeat business.
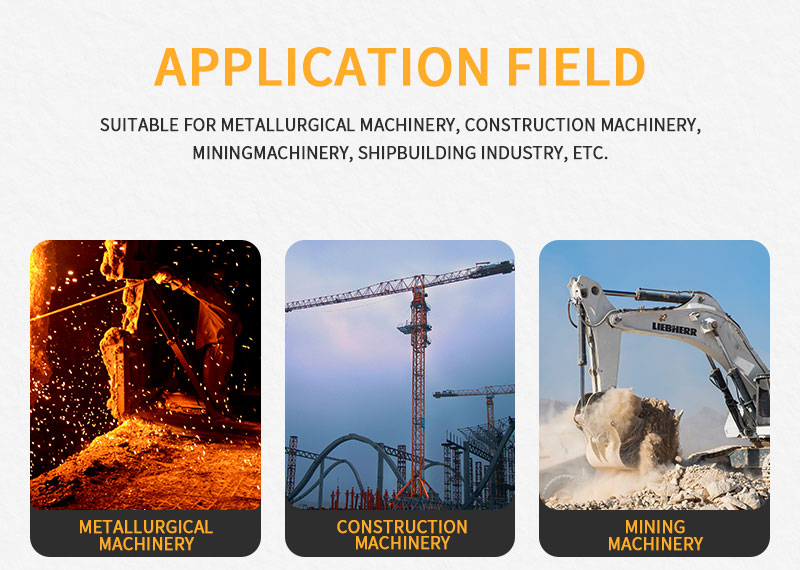
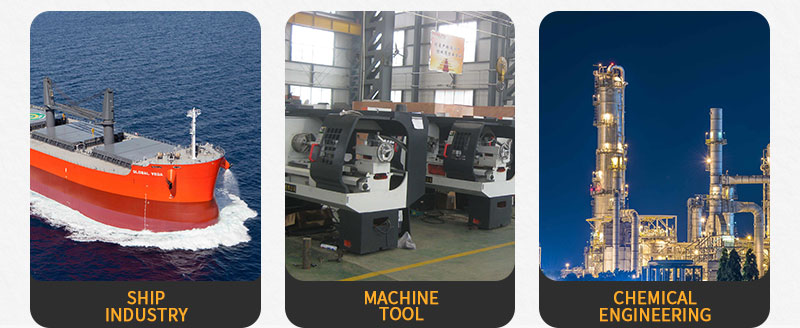