KRR045DLS2131NNN3C2NFA6NPLBNNNNNN high pressure pump
KRR045DLS2131NNN3C2NFA6NPLBNNNNNN high pressure pump
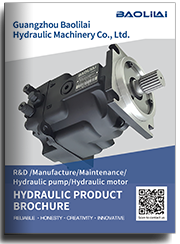
- Product Details
- Applicable Scene
The aerospace sector relies heavily on advanced technologies and precision engineering to ensure safety, efficiency, and reliability. One critical component within this domain is the hydraulic control system, which controls various functions of an aircraft, from flight controls to landing gear operations. At the heart of these systems are hydraulic oil pumps, which provide the necessary fluid power to facilitate these operations. Designing hydraulic oil pumps that meet the stringent requirements of aircraft manufacturing involves a thorough understanding of both hydraulic principles and aerospace industry standards.
KR-R-045D-LS-21-31-NN-N-3-C2NF-A6N-PLB-NNN-NNN
KRR045DLS2131NNN3C2NFA6NPLBNNNNNN
Hydraulic oil pumps must deliver consistent performance under varying operational conditions, including temperature extremes, pressure fluctuations, and the need for high reliability. To achieve this, designers focus on several key aspects:
83023865
Pump Type Selection: The first step in designing a hydraulic pump is selecting the appropriate type. Common types include gear pumps, piston pumps, and vane pumps. Each has its advantages and limitations. For instance, gear pumps are often preferred for their simplicity and ability to generate high pressures, while piston pumps offer better volumetric efficiency and variable displacement capabilities. The choice depends on the specific application within the aircraft system, such as whether high flow rates or precise control is required.
Material Considerations: The materials used in hydraulic pump construction must withstand high pressures, resist corrosion, and maintain integrity under temperature fluctuations. Aerospace applications often utilize lightweight yet durable materials, such as aluminum alloys or composite materials, to reduce overall weight without compromising performance. Additionally, the seals and internal components must be rated for compatibility with the hydraulic fluid, often a specialized oil that meets specific fire-resistant requirements.
Efficiency and Performance: Given the critical nature of aircraft operations, hydraulic pumps must operate with high efficiency to minimize energy consumption and heat generation. This is particularly important in modern aircraft that aim for lower fuel consumption and reduced environmental impact. Engineers employ advanced modeling techniques and computational fluid dynamics (CFD) to design pump geometries that optimize flow characteristics and minimize turbulence, leading to improved efficiency.
Regulatory Compliance: The aerospace industry is governed by stringent regulations that dictate safety and performance standards. Hydraulic oil pumps must comply with standards set by organizations such as the Federal Aviation Administration (FAA) and the European Union Aviation Safety Agency (EASA). This includes rigorous testing procedures to ensure reliability under real-world conditions, including vibration testing, temperature cycling, and pressure endurance tests.
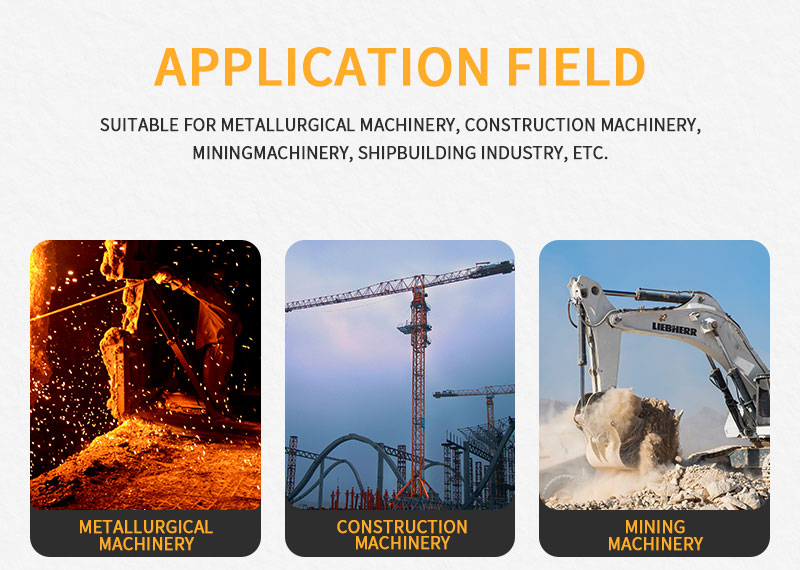
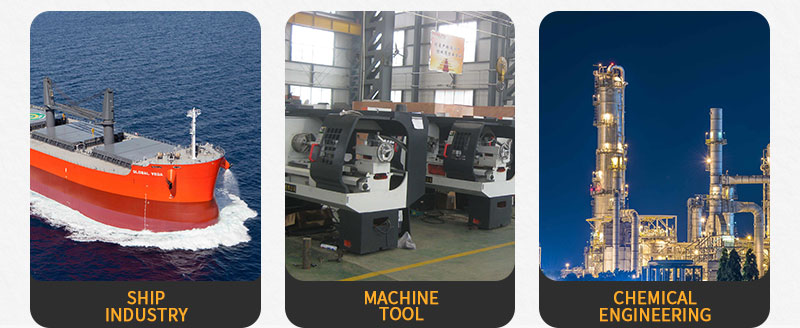