KRR045DLS2120NNN3C3BGA6NPLBNNNNNN hydraulic pump
KRR045DLS2120NNN3C3BGA6NPLBNNNNNN hydraulic pump
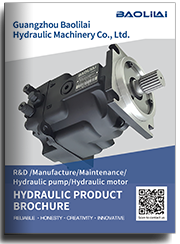
- Product Details
- Applicable Scene
In industrial applications, the need for efficient and reliable chemical injection systems is paramount, particularly in sectors such as oil and gas, chemicals, and water treatment. A crucial component of these systems is the hydraulic oil pump, specifically designed to operate under high-pressure conditions. This article explores the design considerations, types of pumps, and best practices for developing hydraulic oil pumps suitable for high-pressure chemical injection in industrial environments.
KR-R-045D-LS-21-20-NN-N-3-C3BG-A6N-PLB-NNN-NNN
KRR045DLS2120NNN3C3BGA6NPLBNNNNNN
High-pressure chemical injection is crucial for various processes, including enhanced oil recovery, scale prevention, corrosion inhibition, and catalyst transport. The efficacy of these processes relies significantly on the precise delivery of chemicals at the right pressure and flow rates. As such, designing a hydraulic oil pump capable of withstanding high pressures while ensuring optimal performance requires attention to several critical factors.
7004086S
One of the primary considerations in the design of hydraulic oil pumps is the selection of appropriate materials. High-pressure environments exert considerable stress on pump components, making it essential to choose materials that can withstand wear, corrosion, and fatigue. Metals such as stainless steel and alloys with high resistance to chemical degradation are commonly used. Additionally, incorporating advanced coatings can further enhance the durability of the pump components, ensuring a longer operational life.
Another important design aspect is the pump type. There are several categories of hydraulic pumps, including positive displacement pumps and dynamic pumps. Positive displacement pumps, such as gear pumps, diaphragm pumps, and piston pumps, are often favored for high-pressure applications due to their ability to provide constant flow regardless of pressure. The choice of pump type should be guided by the specific requirements of the chemical being injected, including viscosity, temperature, and chemical reactivity.
Pump sizing and configuration are also critical to ensuring effective chemical injection. Engineers must accurately determine the required flow rate and pressure to meet the application’s demands. This involves calculations to account for factors such as system resistance, fluid properties, and the equipment’s overall efficiency. A properly sized pump will not only perform better but also enhance energy efficiency and reduce operational costs.
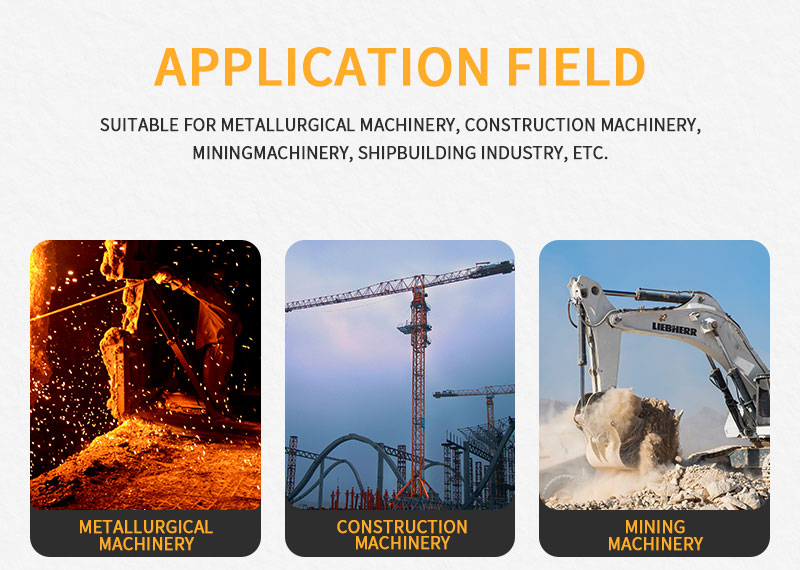
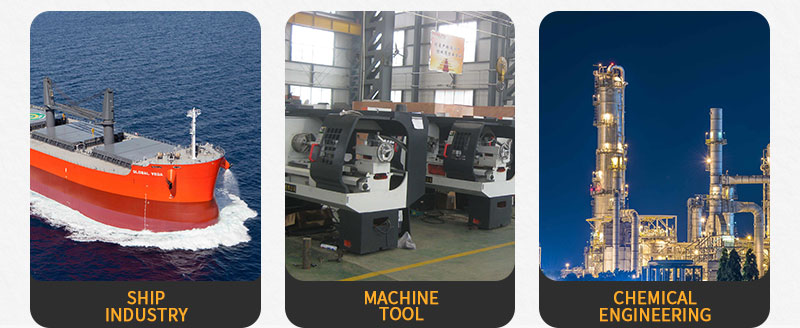