FRL074BPC25NNNNN3K4A2A1NAAANNNNNN high pressure pump
FRL074BPC25NNNNN3K4A2A1NAAANNNNNN high pressure pump
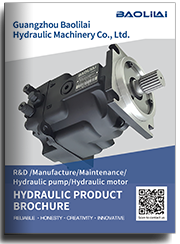
- Product Details
- Applicable Scene
Operating hydraulic pumps in hot environments presents numerous challenges that can significantly affect performance and longevity. Danfoss hydraulic pumps, known for their efficiency and reliability, are not immune to these issues. Understanding these challenges and implementing effective solutions is essential for maintaining optimal operation. This article explores the primary challenges and strategies to overcome them.
FR-L-074B-PC-25-NN-NN-N-3-K4A2-A1N-AAA-NNN-NNN
FRL074BPC25NNNNN3K4A2A1NAAANNNNNN
One of the most significant challenges when operating Danfoss hydraulic pumps in hot environments is the increased temperature of hydraulic fluid. High temperatures can lead to a reduction in the fluid’s viscosity, which can cause a decrease in lubricating properties. This, in turn, increases wear and tear on the pump components, leading to potential failures. To mitigate this issue, it is crucial to regularly monitor fluid temperature and viscosity, ensuring that the hydraulic fluid remains within the manufacturer’s recommended temperature range.
83018104
Another challenge is the degradation of hydraulic fluid over time, particularly in high-temperature environments. Excessive heat can accelerate the oxidation process, resulting in the formation of sludge and varnish that can clog filters and reduce efficiency. To combat this, operators should consider using high-quality hydraulic fluids specifically designed for high-temperature applications. Additionally, implementing a regular maintenance schedule that includes fluid changes and filter replacements can help maintain fluid integrity.
Heat can also impact the seals and hoses used in hydraulic systems. Elevated temperatures can lead to material degradation, resulting in leaks that compromise system efficiency and safety. Selecting heat-resistant materials for seals and hoses can significantly reduce the risk of failure. Regular inspection of these components for signs of wear and replacing them as necessary is a proactive approach to minimizing leaks and maintaining system performance.
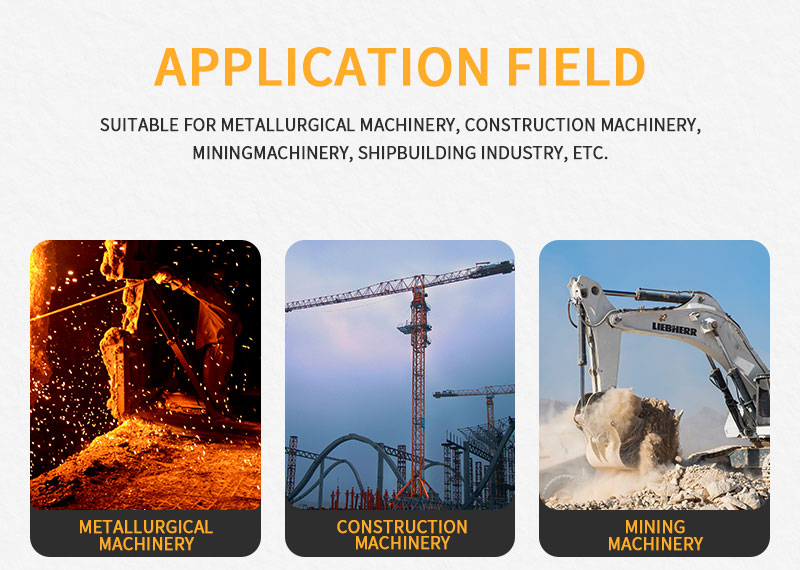
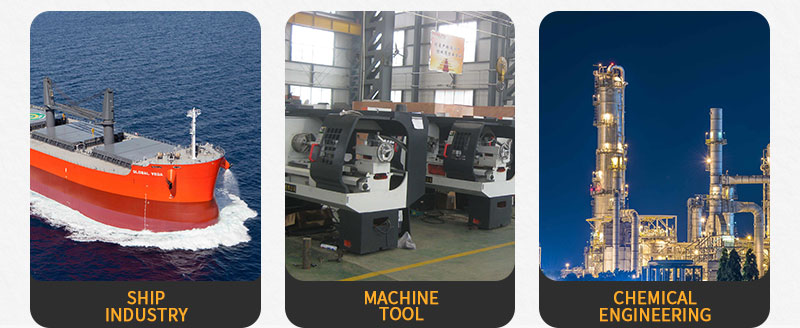