KRR045DLS2120NNN3C3TGA6NPLBNNNNNN high pressure pump
KRR045DLS2120NNN3C3TGA6NPLBNNNNNN high pressure pump
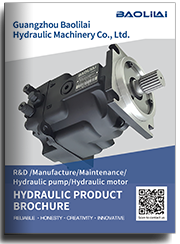
- Product Details
- Applicable Scene
“In today’s oil and gas industry, the demand for high-efficiency and reliable hydraulic systems is ever-increasing. Hydraulic oil pumps play a critical role in optimizing the performance of these systems, particularly in high-pressure applications where precision and reliability are paramount. This article explores key considerations and strategies in designing hydraulic oil pumps tailored for high-pressure oil and gas systems.
KR-R-045D-LS-21-20-NN-N-3-C3TG-A6N-PLB-NNN-NNN
KRR045DLS2120NNN3C3TGA6NPLBNNNNNN
The first step in designing an effective hydraulic oil pump is understanding the specific requirements of the application. High-pressure oil and gas systems often operate under extreme conditions, which necessitate components that can withstand significant mechanical stress, temperature fluctuations, and chemical exposure. Material selection becomes critical; pumps should be constructed from durable materials capable of resisting corrosion and erosion caused by the harsh operating environment. Stainless steel and alloys are commonly used due to their strength and resistance to chemical reactions.
83005974
Next, the design of the pump itself must be carefully considered. The type of pump chosen can greatly influence the overall efficiency and reliability of the system. Positive displacement pumps, for example, can create the necessary pressure to meet the demands of high-pressure applications. They are designed to move a fixed amount of fluid with each cycle, making them suitable for maintaining consistent pressure levels. In contrast, centrifugal pumps, while beneficial in many scenarios, may struggle under high-pressure conditions.
Incorporating advanced engineering techniques in the pump design can enhance performance significantly. Computational fluid dynamics (CFD) simulations can be employed to optimize the internal flow paths of the pump. By analyzing different designs virtually, engineers can predict potential issues and improve performance before prototyping. Additionally, using techniques like finite element analysis (FEA) can help in understanding stress distribution throughout the pump components, allowing for adjustments that improve durability and reliability.
Another important aspect is the design of the sealing mechanisms used in high-pressure hydraulic pumps. Seals must not only prevent leakage but also withstand the high-pressure environment and potential abrasive effects of the hydraulic fluid. Using advanced sealing materials and technologies, such as mechanical seals or cavity seals, can mitigate leakage while enhancing the longevity of the pump.
Additionally, maintenance and accessibility should be considered during the design phase. High-pressure systems often require regular inspections and maintenance to ensure optimal operation. Designing pump components to be easily accessible and modular can reduce downtime and costs associated with maintenance. “
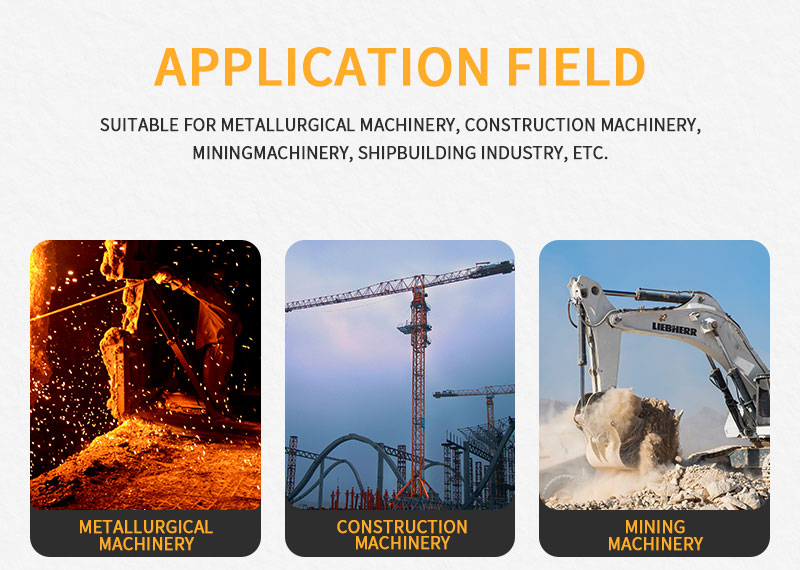
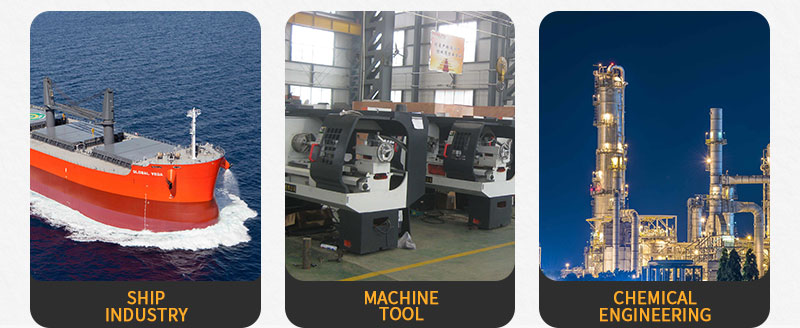