KRR045DLB2120NNN3C2NKA6NKNBNNNNNN sauer danfoss pump
KRR045DLB2120NNN3C2NKA6NKNBNNNNNN sauer danfoss pump
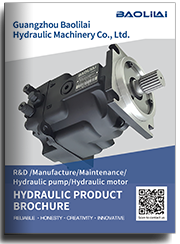
- Product Details
- Applicable Scene
The aerospace industry is known for its uncompromising standards of reliability, efficiency, and performance. At the heart of many of the systems that make modern aircraft function are hydraulic pumps, which provide the necessary power to operate various mechanical components like landing gear, control surfaces, and braking systems. The design of high-pressure hydraulic pumps for aerospace applications presents unique challenges due to the demanding operational conditions and strict regulatory requirements. This article explores the essential considerations and innovations in the design of these critical components.
KR-R-045D-LB-21-20-NN-N-3-C2NK-A6N-KNB-NNN-NNN
KRR045DLB2120NNN3C2NKA6NKNBNNNNNN
One of the primary challenges in designing high-pressure hydraulic pumps for aerospace applications is the need to withstand extreme conditions. These pumps must operate effectively in a wide range of temperatures, pressures, and environmental factors, such as vibrations and altitude variations. This necessitates the use of materials and manufacturing techniques that can endure high operational stresses while maintaining lightweight properties, as weight reduction is crucial in aerospace design.
83052514
Material selection is a key aspect of the design process. Components are typically made from specialized alloys and composite materials that offer high strength-to-weight ratios and corrosion resistance. For instance, titanium and advanced aluminum alloys are often used for their durability and reduced mass. Additionally, surface treatments, such as anodizing or coatings, can enhance the wear resistance of pump components, extending their lifespan and reliability.
Another critical consideration is the pump’s efficiency. Aerospace hydraulic systems demand high power output with minimal energy loss. The design of the pump’s internal geometry must facilitate smooth fluid flow while minimizing turbulence and cavitation, which can lead to damaging pressure fluctuations. Computational fluid dynamics (CFD) simulation is often employed during the design phase to optimize the hydraulic pathways and improve overall efficiency.
Noise and vibration concerns are also paramount in the aerospace industry. High-pressure hydraulic pumps must be designed to operate quietly and with minimal vibration to ensure comfort and safety for passengers and crew. Advanced design techniques, such as finite element analysis (FEA), can predict how components will respond under operational conditions, allowing engineers to make necessary adjustments to mitigate unwanted noise and vibration.
The integration of digital technologies plays a vital role in the modern design process for hydraulic pumps. The use of advanced sensors and real-time monitoring systems can provide valuable data on pump performance, helping engineers make informed decisions about maintenance and operational efficiency. Furthermore, the implementation of Industry 0 principles, such as automation and smart manufacturing, enhances production processes, reduces lead times, and improves quality control.
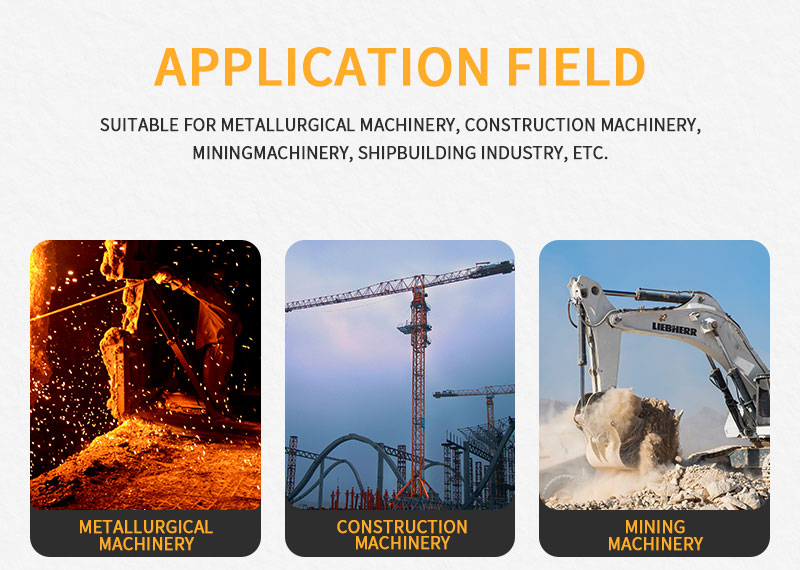
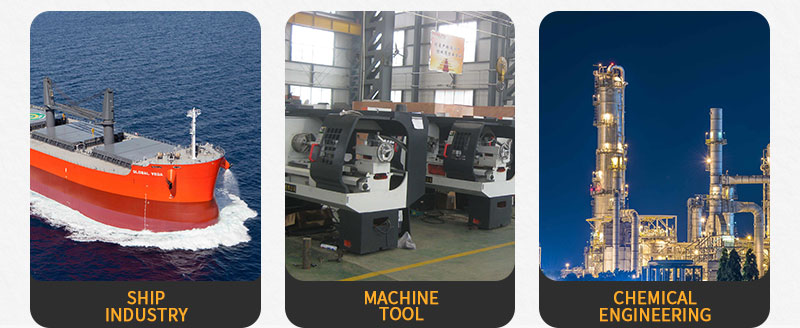